Harriman Material Handling collaborated with CraneWerks to provide Hendrickson, a global leader in commercial transportation solutions, to implement an advanced material handling system that would optimize their production capacity.
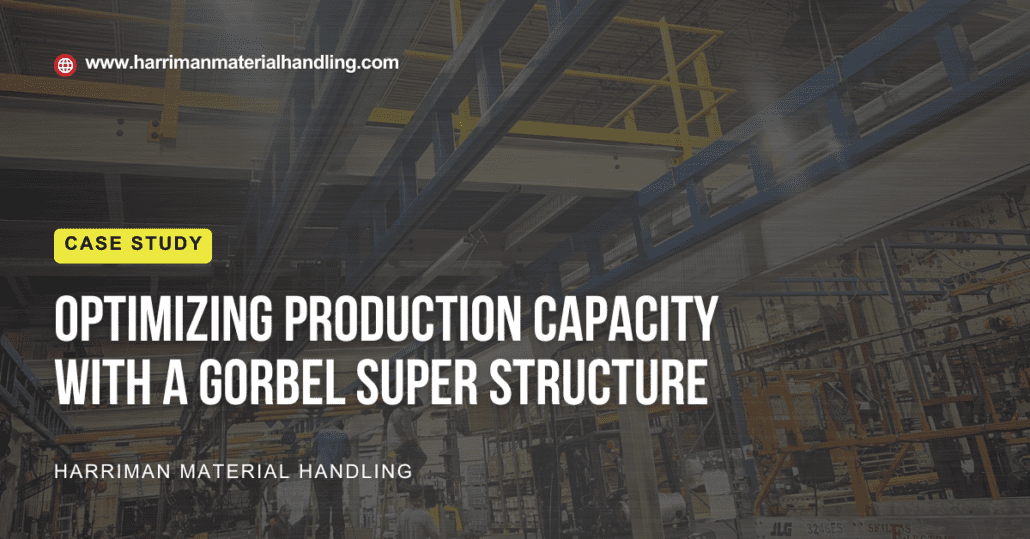
Harriman Material Handling collaborated with CraneWerks to provide Hendrickson, a global leader in commercial transportation solutions, to implement an advanced material handling system that would optimize their production capacity.
This initiative combined Gorbel workstation cranes, CraneWerks’ structural double girder bridge cranes with nested trolleys, a mezzanine, and Magnetek power systems. All these components were harmoniously integrated within a challenging timeline, allowing our dedicated installation team to collaborate amidst ongoing production and multiple contractors.
Hendrickson previously had a CraneWerks and HMH system, which was limited to a single bridge. Before installing the new equipment, we shifted this 6-ton setup using two 3-ton bridge cranes over a weekend to prevent production interruptions.
Our specialists then appended a Gorbel superstructure to the workstation crane’s end, accommodating two bridges. This setup offered a backup, ensuring uninterrupted production even if one crane malfunctioned.
While the crane system was being set up, we simultaneously installed new conveyors, mainly during weekends. Due to the urgency, some tasks were executed during weekdays alongside their active production.
Several challenges arose:
The meticulous design ensured productivity boosts without hampering production. Harriman’s strategy facilitated a versatile integration, minimizing future rewiring or alterations.
System Highlights:
HMH’s teamwork culminated in a robust material handling system, significantly amplifying production capabilities. This underscores the system’s adaptability and growth potential for the client.
Considering material handling advancements? Reach out to Harriman Material Handling for custom, scalable solutions. Let us collaborate to amplify your efficiency while ensuring future-ready growth. Contact us now for tailored insights and quotes.